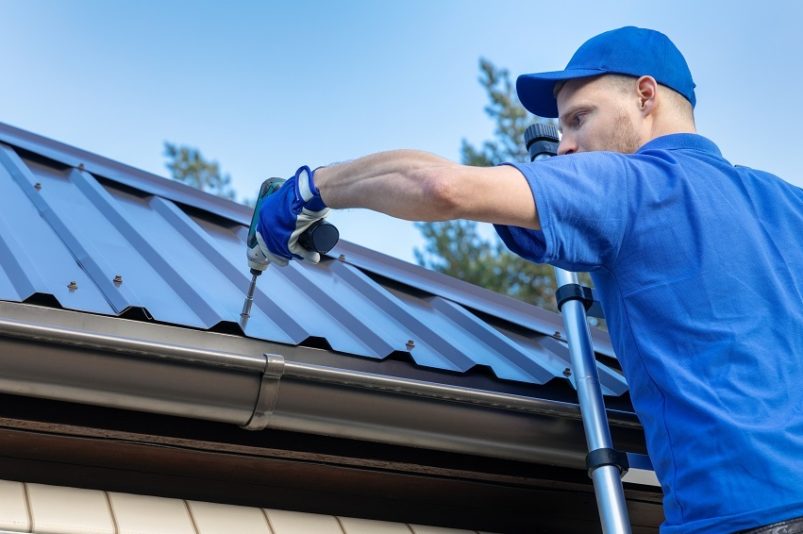
When it comes to roofing, metal is the material of choice for those who value durability, longevity, and style. But a metal roof isn’t just about slapping some panels on top of a building—it’s a complex system where every component must work in harmony. Whether it’s the relentless Texas sun, pounding rain, or heavy snowfall, a well-designed metal roofing system can handle it all.
This post will take you through the core components of a metal roofing system, breaking down what makes each part essential to the overall performance. From the roof deck that forms the foundation to the trims that add those all-important finishing touches, we’ll explore how each piece contributes to a roof that’s built to last.
Roof Deck: The Structural Foundation
In any metal roofing system, the roof deck serves as the bedrock upon which everything else is built. This essential component provides the structural support needed to hold the weight of the roof and withstand various environmental stresses. The roof deck is typically made of wood, plywood, or OSB (Oriented Strand Board) and is crucial for ensuring the metal roofing system’s overall stability and longevity.
For metal roofs, the roof deck must be perfectly level and secure because any imperfections can lead to issues during the installation of the metal panels. A well-prepared roof deck sets the stage for a flawless metal roof installation, ensuring that the panels lay flat and the entire system remains watertight.
Underlayment: The Vital Protective Barrier
Underlayment is a critical component in metal roofing systems, providing an extra layer of protection between the roof deck and the metal panels. Its primary function is to prevent water infiltration, serving as a backup defense if water ever manages to get past the metal panels. Additionally, underlayment helps with noise reduction and adds an extra layer of insulation.
There are different types of underlayment used in metal roofing, including synthetic and self-adhering membranes. Synthetic underlayment is often preferred in metal roofing due to its superior durability and resistance to tearing. It’s specifically designed to handle the expansion and contraction of metal, which occurs as temperatures fluctuate.
Important Note: In a metal roofing system, the underlayment must be of high quality to handle the unique stresses that metal roofs endure, such as thermal movement and potential condensation issues.
Metal Panels: The Heart of the Roof
The metal panels are the most visible and defining component of a metal roofing system. These panels are what give the roof its distinctive look and provide the primary barrier against the elements. Metal panels are available in various materials, including steel, aluminum, copper, and zinc, each offering different benefits in terms of durability, aesthetics, and cost.
The installation of metal panels requires precision. They must be properly aligned and secured to ensure that the roof is not only watertight but also capable of withstanding wind uplift and other forces. The choice of panel style, whether standing seam, corrugated, or another design, will also influence the overall performance and appearance of the roof.
Fasteners and Caps: The Backbone of a Secure Metal Roof
Fasteners and caps might seem like small details, but they are the unsung heroes that keep a metal roof in place. When it comes to metal roofing, you can’t just use any old screws—you need fasteners specifically designed to handle the job. These are usually self-tapping screws made from galvanized steel or stainless steel, built to resist corrosion and hold up against the elements.
The key to a solid metal roof is making sure these fasteners are installed correctly. They have to be driven in straight and snug, but not so tight that they warp the metal panels or damage the seal. And that’s where the caps come in—they cover the heads of the fasteners, creating a watertight seal that keeps moisture out. Without these, you could end up with leaks that compromise the entire system.
Think of fasteners and caps as the backbone of your metal roof. Without them, the panels would shift, the wind could catch an edge, and before you know it, you’re dealing with a roof that’s more of a headache than a shelter.
Flashing: The Ultimate Defender Against Leaks
Flashing is one of those things that doesn’t get a lot of attention until it’s not working right—then it’s all you can think about. Good flashing is all about precision. It has to be cut and bent to fit perfectly around whatever it’s protecting, and then it’s sealed up tight to make sure there’s no way for water to get through. The most common material for flashing in metal roofs is galvanized steel or aluminum, both of which are chosen for their durability and corrosion resistance.
One of the most important types of flashing is the drip edge. It’s installed along the edges of the roof, guiding water off the roof and into the gutters instead of letting it run down the side of your building, which could cause damage over time.
Ridge Cap: The Finishing Touch That Protects the Peak
This is the piece that covers the peak of your roof, where two slopes meet. Without a ridge cap, that seam would be a prime spot for water to get in and wreak havoc.
In metal roofing, the ridge cap isn’t just about keeping water out; it also plays a role in ventilation. Many ridge caps are designed to allow air to flow through the attic, helping to keep the roof system cool and dry. This is particularly important in metal roofs because proper ventilation can prevent issues like condensation, which could otherwise lead to rust or mold over time.
Installing a ridge cap requires careful alignment and fastening, just like the metal panels themselves. It needs to fit perfectly along the roof’s peak, creating a tight seal that stands up to wind, rain, and anything else Mother Nature decides to throw its way.
Sealants and Closure Strips: The Final Line of Defense
Sealants and closure strips are like the silent protectors of your metal roof, working behind the scenes to keep everything airtight and watertight. Even though metal panels and flashing do most of the heavy lifting, there are always tiny gaps and seams where water or air could sneak through—this is where sealants and closure strips come in.
Sealants are applied along seams, around fasteners, and in any place where two materials meet. The goal is to create a flexible barrier that can expand and contract with the metal as it heats up and cools down. In metal roofing, the most common types of sealants are butyl tape and silicone-based sealants. Butyl tape is often used in the overlaps of metal panels, while silicone is more flexible and durable, making it ideal for joints and edges.
Closure strips, on the other hand, are used to fill the gaps at the edges of metal panels, particularly where the panels meet the ridge cap, eaves, or any other transition points. They’re usually made of foam or rubber and are designed to match the profile of the metal panels. These strips are crucial for keeping out water, wind, and even pests, ensuring that your metal roof remains secure and leak-free.
Think of sealants and closure strips as the final line of defense. Without them, even the most perfectly installed metal roof would be vulnerable to leaks and drafts, undermining all the work that went into the rest of the system.
Vents and Ventilation Systems: Breathing Life into Your Roof
Ventilation is one of those things that might not be top of mind when you think about a metal roof, but it’s actually vital to the health of the entire system. Proper ventilation keeps the roof—and the space below it—cool, dry, and free of excess moisture, which is key to preventing issues like mold, rust, and even ice dams in colder climates.
In a metal roofing system, ridge vents are often used in conjunction with the ridge cap. These vents run along the peak of the roof, allowing hot air to escape from the attic while pulling in cooler air through soffit vents at the roof’s edges. This continuous airflow helps regulate the temperature and moisture levels inside the attic, which can have a big impact on the lifespan of your roof and even the energy efficiency of your home.
Another common type of ventilation in metal roofs is gable vents, which are installed in the walls near the roof’s peak. These vents work with the ridge and soffit vents to create a balanced ventilation system that keeps air moving freely through the attic space.
Trims: The Finishing Touches That Pull It All Together
Trims might seem like just decorative pieces, but they actually play a crucial role in the performance of a metal roofing system. Trims are installed along the edges, corners, and joints of the roof, providing a finished look while also helping to protect against water infiltration and wind uplift.
There are several types of trims used in metal roofing, including eave trims, gable trims, and valley trims. Eave trims run along the lower edge of the roof, guiding water into the gutters and preventing it from dripping back onto the structure. Gable trims cover the vertical edges of the roof, where the panels meet the wall, ensuring a clean, finished appearance and sealing off any gaps. Valley trims are used where two roof slopes meet, directing water down to the gutters and away from the roof.
Trims are usually made from the same material as the metal panels so that they match in both appearance and durability. When installed correctly, trims not only enhance the visual appeal of the roof but also add an extra layer of protection, helping the entire roofing system function more effectively.
The Sum of Its Parts
From the roof deck that provides the foundation to the fasteners that hold everything in place, each element must work together seamlessly to protect the building. In metal roofing, it’s the attention to detail that makes all the difference. When each component is chosen carefully and installed with precision, the result is a roof that not only looks great but also stands the test of time, providing reliable protection for years to come.